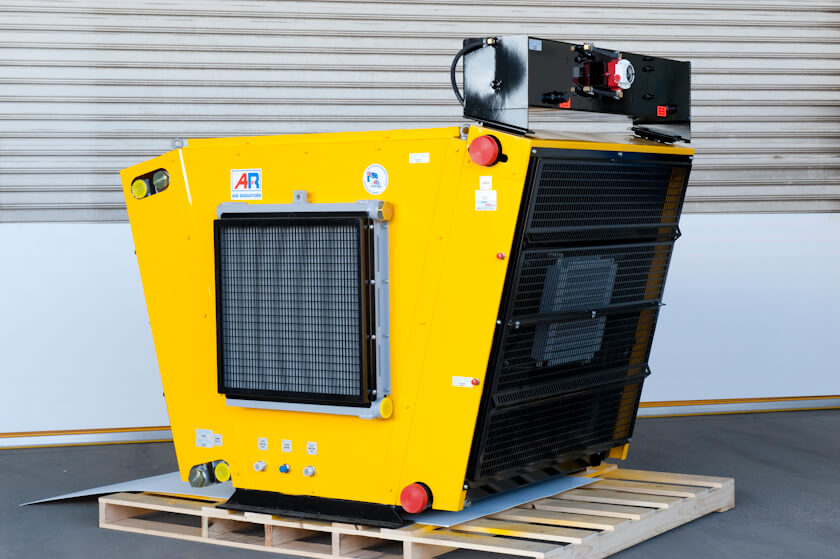
Air Radiators offer Dry Coolers as a closed loop solution to the traditional high maintenance Evaporative Cooling Tower, eliminating plume, water consumption and bacterial growth, and reducing running and maintenance costs. This technology allows for cooling of glycol/water-based mixtures taking advantage of the ‘free cooling’ offered during low ambient conditions. Module or bays can easily be added or removed from the design, and high efficiency fan and drive systems ensure noise and parasitic power is limited during operation.
Air Radiators Dry Coolers are available in:
- Vertical Configurations
- Horizontal Configurations
- ‘V’ Configurations
Adiabatic Cooling
- Evaporative Pre Cooler pads reduce temperature of the ambient air approaching radiator
- Enables radiator to supply water back to the process at a much lower temperature
WHY ARE pre-coolers important?
- Ambient air passing through the Pre Cooler is cooled by contact with the wetted pad surfaces of the Pre Cooler panels
- Better performance to operate in higher ambient conditions
- Reduced operating costs and long life
- Use significantly less water
- Compact and self-contained designs
- Automatically activate only when require and are not breeding grounds for Legionella bacteria
Remote series
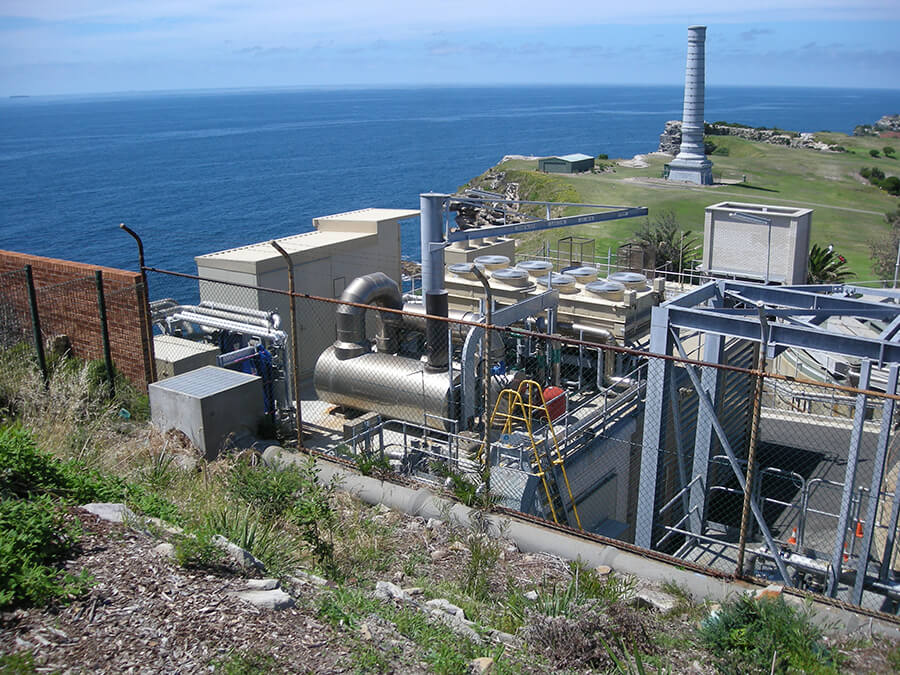
The Horizontal Remote Series range of coolers is suited to a wide variety of applications. Our integrated design philosophy ensures flexibility for different heat transfer surfaces, suitable for water, oil, compressed air and process fluids.
The draw-through fan design maximizes fan efficiencies, and ensures optimal cooler performance meeting today’s environmental requirements for low noise levels and reduced parasitic power (fan) levels.
The modular construction of our Horizontal Remote Coolers ensures easy maintenance and service activities throughout the extended service life.
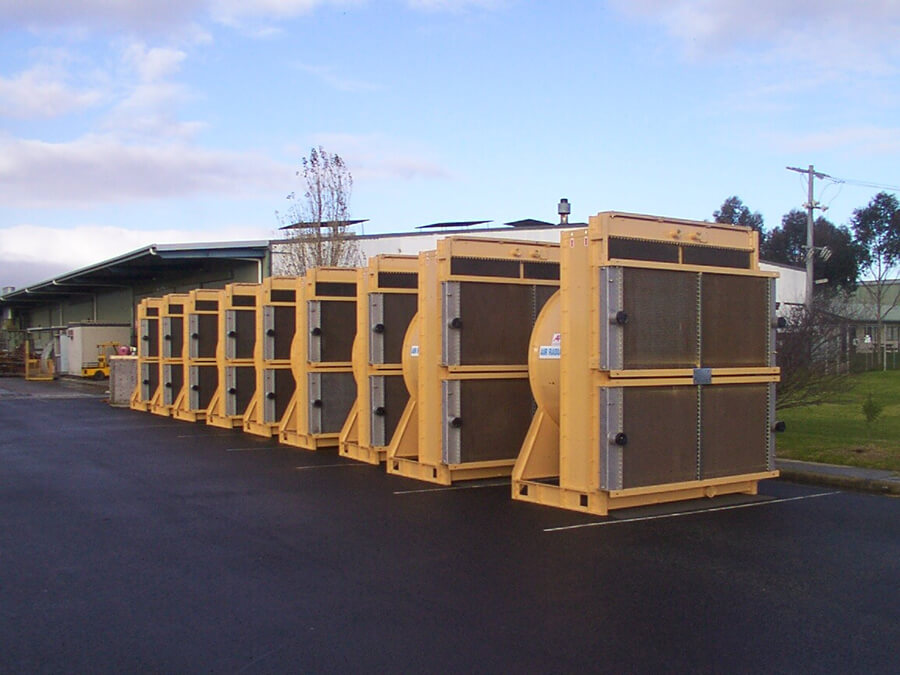
The Vertical Remote Series represents a range of cooling modules able to incorporate heat transfer surfaces suitable for water, oil, compressed air and process fluids.
The ‘blow through’ design employs a duct-mounted fan providing maximum fan efficiency and thus the scope to cater for additional air side resistance, as encountered in canopies, plant rooms and noise-attenuated installations.
The robust construction and innovative design provides flexibility in installation, whether by direct mounting to the engine skid, wall-mounted or, alternatively in a free standing situation. With all products – servicing requirements are addressed at the design stage incorporating modular construction methods to allow easy access for work infield.
SKID MOUNTED
Applications such as stationary diesel-driven generator sets and pumps require reliable and compact cooling systems.
Air Radiators offers Skid Mounted cooling packages that incorporate fit-for-purpose design features, ease of installation and low maintenance.
Using a modular design platform, we can provide packaged cooling systems with a high degree of customization. Design scope includes:
- Engine jacket water
- Engine intercooler circuit
- Direct charge air-to-air cooling
- Fuel cooling
- Fan and fan belt cowling
- Fan and core guarding
- Plumbing kits
- De-aeration system – external and integral
- Fan impeller and fan pulley spacer
The combination of highly refined design tools and vast experience allows the company to deliver innovative cooling solutions for all diesel driven industrial applications
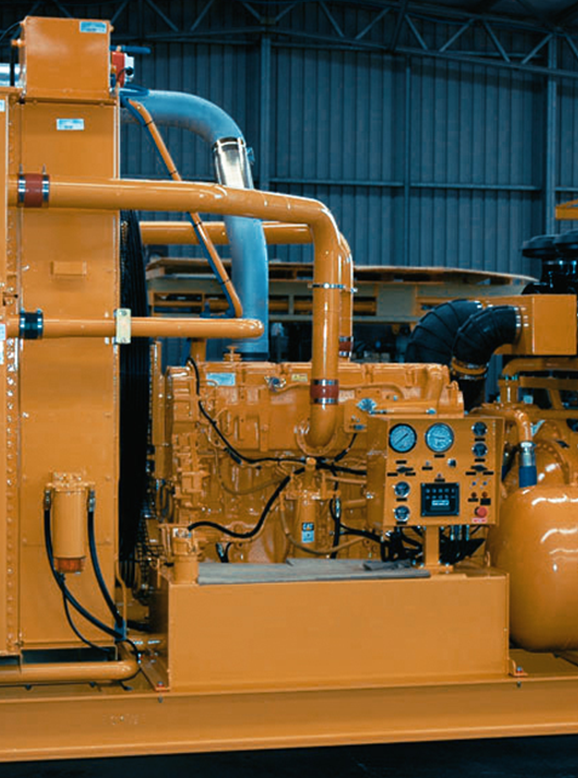
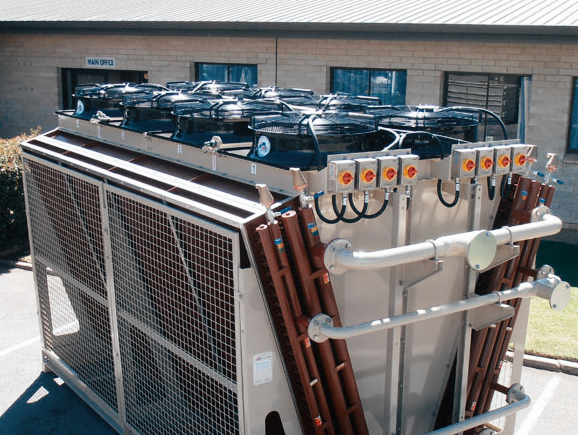
V-PACK
Able to be set up with a variety of heat transfer matrices, the V-Pack configuration is a versatile solution for process cooling applications. Various processes such as compressed gas flow, and compressor oil flow can be cooled in a single module, while maintaining complete segregation and redundancy of each circuit.
Space constraints often seen in offshore applications can be overcome through the features offered by the V-Pack’s design. The high cooling density offered by the inclined panel design can fulfill duties previously thought unrealistic in small spaces, therefore offering solution in difficult installations.
ELECTRIC MOTOR
Large electric motor and electrical alternators often use water-to-air heat exchangers in order to keep electrical windings within temperature limitations.
These heat exchangers or “coolers” are usually housed near the motor or alternator and ventilation airflow, generated by fan blades attached to the rotor shaft, is passed through the coolers to facilitate heat transfer. Water or a similar coolant is circulated through the heat exchanger to transfer collected heat from air to the coolant.
While efficient operation of these coolers is paramount to maintaining winding temperatures, the coolers are regularly exposed to unique operating conditions that require an innovative and flexible approach to heat exchanger design. Design considerations include:
- 20-plus years of service life
- Untreated coolants (corrosive, chemically aggressive, dissolved and undissolved solids)
- Vibration
- Extended service periods
- Thermal stresses
The threat posed by a vessel leaking coolant near large electrical equipment is a significant driver in the design of coolers that are not only thermally efficient, but also extremely robust.
Air Radiators has more than 40 years’ experience in the design and manufacture of coolers for this unique and challenging application.
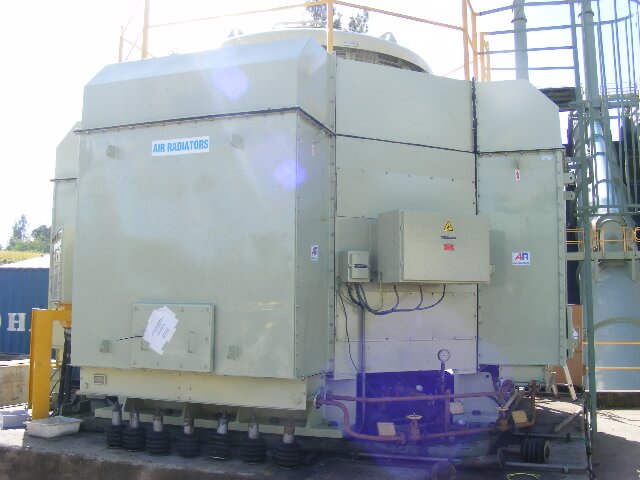